Solder balling, a common concern in PCB assembly, refers to the unintended formation of spherical balls of solder during the reflow process, often leading to connectivity issues and potential short circuits. Understanding the root causes, potential effects, and effective solutions for resolving solder balling issues is crucial for maintaining the integrity and functionality of printed circuit boards.
In this comprehensive exploration, we will delve into the underlying causes of solder balling, analyze its potential impacts on PCBs, and provide practical strategies and best practices for preventing and addressing solder balling challenges in PCB assembly.
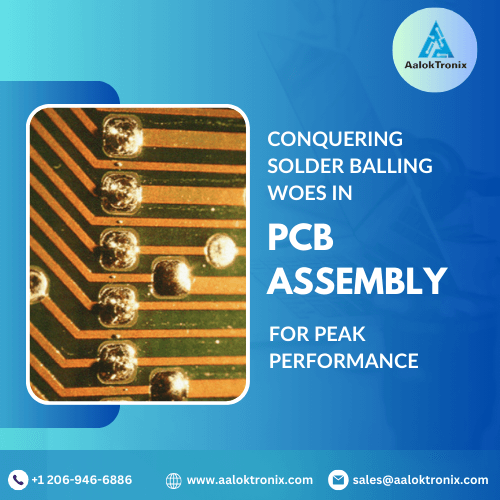
Causes of Solder Balling:
Solder balling can result from various factors, including excessive solder paste application, inappropriate reflow profiles, or the presence of contaminants on the PCB surface.
Factors such as uneven solder paste distribution, inadequate stencil design, or improper reflow temperature profiles can contribute to the formation of solder balls, leading to potential short circuits and compromised electrical connections between the soldered components and the PCB pads.
Impacts of Solder Balling on PCBs:
The presence of solder balls can have significant implications on the functionality and reliability of PCBs, particularly in terms of electrical connectivity and signal integrity.
Solder balling can lead to unintended electrical connections between neighboring components, resulting in potential short circuits, signal interference, or voltage fluctuations.
Furthermore, solder balls can impede the mechanical stability of the PCB assembly, leading to poor shock and vibration resistance, increased susceptibility to mechanical stress, and potential mechanical failures during the operation of the electronic device.
Identifying Solder Balling:
Identifying solder balling requires a meticulous visual inspection of the soldered joints and the PCB assembly, focusing on the presence of spherical or irregularly shaped solder deposits between the soldered components and the PCB pads.
Soldered joints affected by solder balling typically exhibit the presence of excess solder residues or irregular solder formations, resembling spherical or irregularly shaped balls, indicating potential solder bridging or short circuit risks.
Utilizing magnification tools, such as magnifying lenses or digital microscopes, can aid in the accurate identification and assessment of solder balling during the inspection process.
Best Practices for Managing Solder Balling:
To manage the risks of solder balling and ensure reliable solder connections in PCB assembly, implementing targeted best practices and preventive strategies is crucial throughout the soldering process. Implementing controlled solder paste application techniques, such as optimized stencil designs or precise solder paste dispensing, can aid in regulating the solder volume and promoting uniform solder distribution, reducing the likelihood of solder balling and subsequent short circuit risks.
Optimizing the reflow temperature profiles and ensuring compatibility with the solder paste and PCB material specifications can aid in achieving the ideal balance between sufficient heat transfer and controlled solder flow, minimizing the risk of solder balling and promoting the formation of reliable solder connections.
Implementing advanced reflow soldering technologies, such as nitrogen reflow or vapor phase soldering, can provide more precise control over the soldering environment and minimize the risk of solder balling, particularly for complex PCB assemblies or components with high thermal mass.
Conducting comprehensive solderability tests and quality control inspections can further enhance the detection and prevention of solder balling issues, ensuring the production of high-quality, defect-free PCB assemblies and electronic products.
Conclusion:
In conclusion, comprehensively understanding the challenges of solder balling in PCB assembly is pivotal for ensuring the reliability and performance of electronic devices and systems. By addressing the root causes, assessing the implications, and adopting best practices and preventive strategies, manufacturers and electronics enthusiasts can significantly enhance the soldering quality and integrity of their PCB assemblies, contributing to the development of robust, high-functioning electronic applications and technologies.