A cold joint in the context of PCB soldering refers to an imperfect solder connection that occurs due to inadequate heat transfer during the soldering process.
It’s crucial to grasp the intricacies of this common issue to ensure the overall integrity and functionality of printed circuit boards.
In this comprehensive guide, we will delve into the root causes of cold joints, examine their detrimental effects on PCBs, and provide effective remedies and preventive measures to avoid their occurrence.
Causes of Cold Joints:
The primary cause of cold joints lies in insufficient heat application during the soldering process.
When the soldering iron’s temperature is too low or when it isn’t in contact with the joint for an adequate duration, the solder fails to melt completely, leading to an imperfect bond between the component lead and the PCB pad.
Moreover, factors like incorrect soldering iron settings, poor-quality solder, and inadequate flux application can contribute to the formation of cold joints.
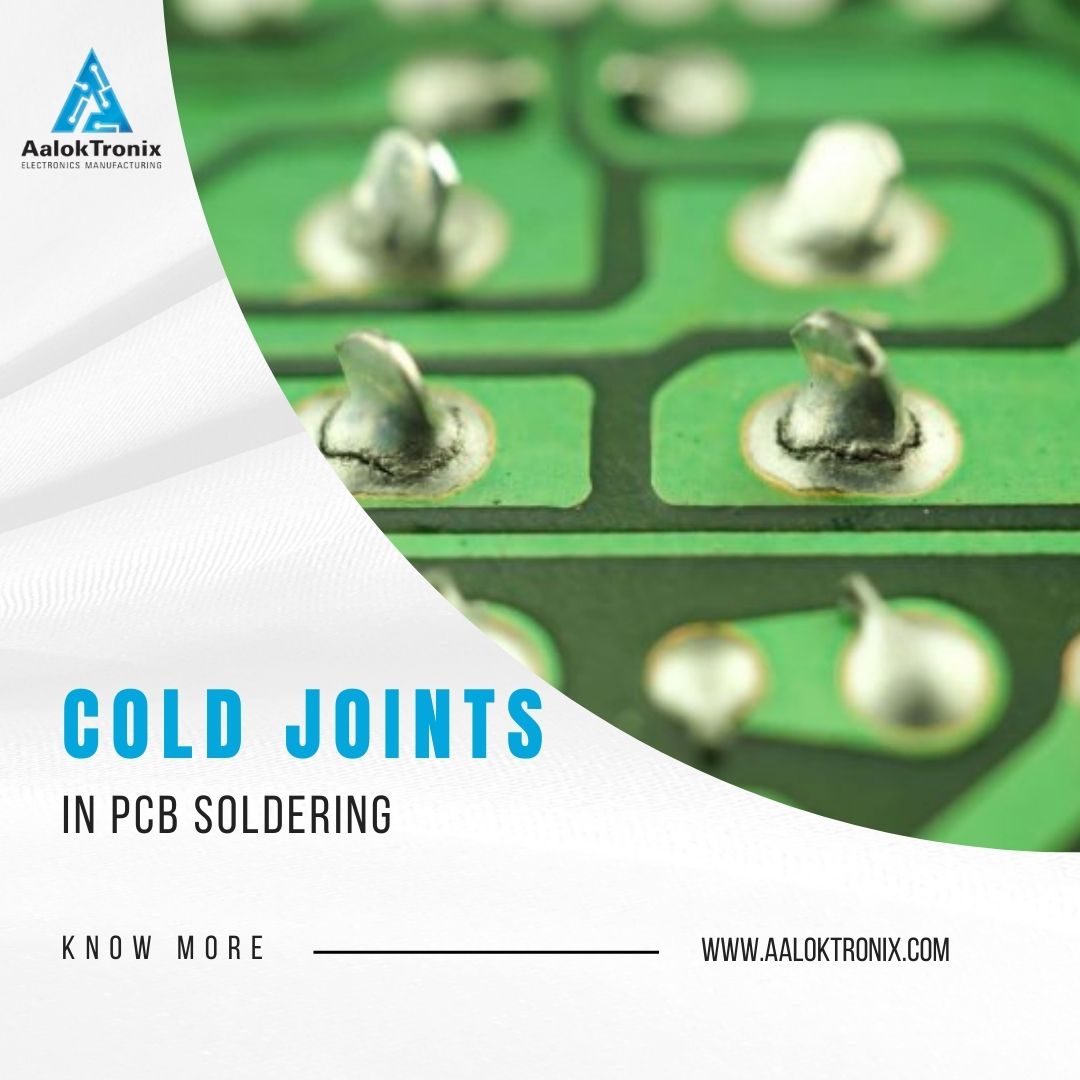
Effects of Cold Joints on PCBs:
The presence of cold joints can have severe ramifications on the performance and reliability of PCBs.
In terms of electrical conductivity, a cold joint can result in increased resistance, leading to signal distortion, voltage fluctuations, and potential circuit failures.
This compromised electrical connection can further contribute to overheating, component malfunction, or complete system failure, particularly in complex electronic devices and sensitive applications.
Identifying Cold Joints:
Identifying cold joints requires a keen eye and a thorough understanding of the physical characteristics of a properly soldered joint.
In contrast to a well-executed joint, a cold joint typically exhibits a dull, grainy appearance, with an uneven surface texture and a visibly porous structure.
Additionally, cold joints may appear lighter in color compared to properly soldered connections, indicating incomplete fusion and a lack of metallurgical bonding between the solder and the surfaces.
Remedies and Prevention Strategies:
To mitigate the occurrence of cold joints, several effective remedies and preventive measures can be implemented during the soldering process.
Firstly, ensuring the use of an appropriate soldering iron temperature, typically within the recommended range specified by the solder manufacturer, is crucial.
Additionally, allowing sufficient contact time between the soldering iron and the joint, as well as using high-quality solder and flux, can facilitate optimal heat transfer and promote the formation of robust, reliable solder connections.
Moreover, adopting proper soldering techniques, such as maintaining a steady hand, using the right amount of solder, and applying flux adequately, is instrumental in preventing the formation of cold joints.
Employing preheating methods, such as the use of preheaters or hot air stations, can also aid in enhancing heat transfer and reducing the risk of cold joint formation, particularly when dealing with complex PCB assemblies or components with high thermal mass.
Conclusion:
In conclusion, comprehending the intricacies of cold joints in PCB soldering is paramount for ensuring the durability and functionality of electronic devices and systems.
By recognizing the root causes, effects, and identification techniques, as well as implementing effective remedies and preventive measures, manufacturers and electronic enthusiasts can significantly improve the quality and reliability of their PCB soldering processes, ultimately leading to the development of robust, high-performance electronic products and applications.