Introduction:
Prototype PCB assembly plays a crucial role in the development of electronic devices and gadgets. It involves the process of transforming circuit designs into physical printed circuit boards (PCBs) for testing and evaluation before mass production.
In this blog post, we will delve into the world of prototype PCB assembly, covering everything from the initial design phase to the final manufacturing steps.
Whether you’re a hobbyist, a startup founder, or an engineer working on a new product, this guide will provide you with valuable insights into creating functional prototypes efficiently and effectively.
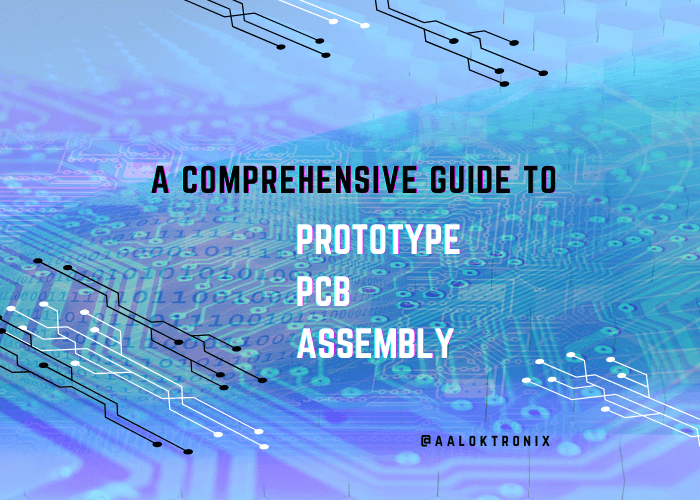
1. Understanding Prototype PCB Assembly:
Prototype PCB assembly is the process of transforming circuit designs into physical printed circuit boards (PCBs) for testing and evaluation before mass production. In this section, we’ll explore the significance of prototype assembly, its benefits, and the common challenges you may encounter during the assembly process.
- Definition and significance of prototype PCB assembly: Learn about the purpose and importance of prototype assembly in the development process, allowing you to test and refine your circuit designs before moving to mass production.
- Benefits of prototyping before mass production: Discover the advantages of prototyping, including risk reduction, cost savings, and the ability to identify and address design flaws early on.
- Common challenges and considerations during the assembly process: Explore the potential hurdles that may arise during prototype PCB assemblies, such as component availability, manufacturing complexities, and design compatibility.
2. PCB Design Considerations:
Effective PCB design is crucial for successful prototype assembly. In this section, we’ll cover key considerations such as component selection, footprints, and design for manufacturability (DFM) guidelines. Understanding these factors will ensure that your PCB design is optimized for assembly and manufacturing.
- Key design considerations for prototype PCBs: Understand the essential factors to keep in mind when designing a prototype PCB, including component selection, footprint placement, signal integrity, power distribution, and thermal management.
- Selecting the right components and footprints: Learn how to choose appropriate components and footprints based on your design requirements, taking into account factors like functionality, availability, cost, and compatibility with assembly processes.
- Design for manufacturability (DFM) guidelines: Gain insights into designing PCBs that are optimized for efficient assembly and manufacturing, ensuring that your prototypes can be easily reproduced on a larger scale.
3. PCB Manufacturing Methods:
There are various methods available for manufacturing PCBs, each with its own pros and cons. This section provides an overview of different manufacturing methods, such as etching, milling, and printing, and helps you choose the most suitable method for your prototype based on your requirements and resources.
- Overview of different PCB manufacturing methods: Explore various manufacturing methods such as etching, milling, and printing, and understand their respective advantages, limitations, and suitability for different types of prototypes.
- Exploring the pros and cons of each method (e.g., etching, milling, printing, etc.): Delve deeper into the benefits and drawbacks of each manufacturing method, considering factors such as complexity, accuracy, speed, cost, and the type of circuit design you are working with.
- Choosing the most suitable manufacturing method for your prototype: Evaluate your project requirements, resources, and budget to make an informed decision about the best manufacturing method to use for your specific prototype.
4. Component Sourcing and Procurement:
Sourcing the right components for your prototype assembly is vital. In this section, we’ll discuss tips for sourcing components, managing lead times, and evaluating suppliers. Additionally, we’ll address the challenge of component obsolescence and how to mitigate its impact on your assembly process.
- Tips for sourcing components for prototype assembly: Discover strategies for finding and selecting the right components for your prototype, including reliable suppliers, availability of components, and considerations for lead times.
- Understanding component availability and lead times: Learn how to manage component availability challenges and minimize lead times, ensuring that you have the necessary components in a timely manner to proceed with your prototype assembly.
- Evaluating suppliers and managing component obsolescence: Gain insights into evaluating component suppliers, assessing their reliability and quality, and mitigating risks associated with component obsolescence through proactive planning and alternative sourcing options.
5. Prototype Assembly Techniques:
This section dives into the assembly process itself, focusing on surface mount technology (SMT) and through-hole assembly. We’ll guide you through the step-by-step process of assembling your prototype, including the necessary tools and equipment you’ll need for efficient and accurate assembly.
- Introduction to surface mount technology (SMT) and through-hole assembly: Understand the basics of both SMT and through-hole assembly techniques, their differences, and when each method is most appropriate for your prototype.
- A step-by-step guide to the prototype assembly process: Follow a comprehensive walkthrough of the prototype assembly process, covering tasks such as solder paste application, component placement, reflow soldering, through-hole soldering, cleaning, and inspection.
- Tools and equipment required for efficient assembly: Learn about the essential tools and equipment needed for prototype assembly, including soldering stations, reflow ovens, inspection tools, and more, ensuring you have the necessary resources for successful assembly.
6. PCB Testing and Debugging:
Testing and debugging are essential to ensure the functionality and reliability of your prototype. In this section, we’ll emphasize the importance of testing methodologies such as visual inspection and functional testing. We’ll also explore common issues that may arise during testing and provide tips for effective troubleshooting.
- Importance of testing and debugging prototypes: Understand why thorough testing and debugging are vital to ensure the functionality, performance, and reliability of your prototypes before moving forward with production.
- Overview of testing methodologies (e.g., visual inspection, functional testing, etc.): Explore different testing methodologies, such as visual inspection, functional testing, boundary scan, and in-circuit testing, and determine the most suitable approach for your prototype.
- Troubleshooting common issues and improving design iterations: Gain insights into common problems that may arise during testing, and learn how to effectively troubleshoot and address issues to refine your design and enhance the prototype’s performance.
7. Iterative Prototyping and Design Optimization:
Iterative prototyping allows you to refine your design based on feedback and improve its performance, reliability, and manufacturability. This section delves into the role of iterative prototyping, gathering feedback effectively, and implementing design improvements for a more robust and efficient prototype.
- The role of iterative prototyping in product development: Discover the iterative prototyping approach and how it allows for incremental improvements, incorporating feedback, and optimizing your design for better performance, reliability, and manufacturability.
- Gathering feedback and implementing design improvements: Learn strategies for gathering feedback from stakeholders, users, and experts, and leveraging that feedback to identify areas of improvement and implement design modifications in subsequent iterations.
- Optimizing for performance, reliability, and manufacturability: Explore techniques to optimize your design based on performance metrics, reliability considerations, and manufacturability requirements, ensuring that your prototype is refined and ready for mass production.
8. Transitioning to Mass Production:
When your prototype is ready, transitioning to mass production requires careful consideration. In this section, we’ll discuss the factors to consider when scaling up production, collaborating with contract manufacturers (CMs), and maintaining quality and cost-efficiency throughout the transition from prototype to mass production.
- Considerations when transitioning from prototype to mass production: Understand the factors to consider when scaling up production, including cost analysis, supplier management, quality control, and logistics planning, to ensure a smooth transition from prototype to large-scale manufacturing.
- Collaborating with contract manufacturers (CMs): Explore the benefits of partnering with electronics contract manufacturers and the considerations involved in selecting the right CM for your production needs, including capabilities, experience, certifications, and communication channels.
- Scaling up production while maintaining quality and cost-efficiency: Learn strategies to scale up production while maintaining product quality, optimizing costs, and implementing efficient manufacturing processes to meet market demand effectively.
Conclusion:
Prototype PCB assembly is a critical phase in the product development process. By following best practices and understanding the intricacies of design, manufacturing, and testing, you can streamline your prototype assembly process and accelerate your path to a successful product launch. With this comprehensive guide, you now have the knowledge and tools to embark on your prototype PCB assembly journey with confidence.