Corrosion, a persistent challenge in PCB assembly, refers to the gradual degradation or oxidation of metal components and traces on the PCB, leading to compromised electrical connectivity and potential system failures.
Understanding the root causes, potential effects, and effective preventive measures for combating corrosion is essential for maintaining the reliability and functionality of electronic devices.
In this comprehensive exploration, we will delve into the underlying causes of corrosion, analyze its potential impacts on PCBs, and provide practical strategies and best practices for preventing and addressing corrosion-related issues in PCB assembly.
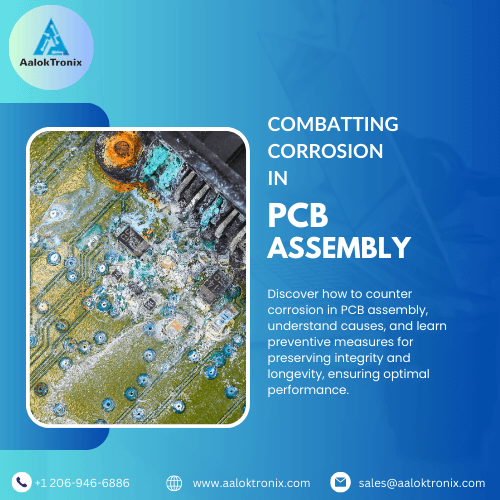
Causes of Corrosion:
Corrosion can arise from various factors, including exposure to moisture, environmental contaminants, or improper storage conditions during the PCB manufacturing and assembly processes.
Factors such as high humidity levels, the presence of reactive chemicals, or inadequate conformal coating application can contribute to the onset of corrosion, leading to the deterioration of metal surfaces and the gradual degradation of the PCB’s electrical and structural integrity.
Impacts of Corrosion on PCBs:
The presence of corrosion can have significant implications on the performance and longevity of PCBs, particularly in terms of electrical conductivity and signal integrity.
Corrosion can lead to increased electrical resistance, signal attenuation, or complete circuit failures, resulting in compromised functionality and reduced operational efficiency of the electronic device.
Furthermore, the spread of corrosion can lead to the degradation of the PCB’s mechanical stability, leading to poor shock and vibration resistance, increased susceptibility to environmental factors, and potential structural failures during the device’s lifecycle.
Identifying Corrosion:
Identifying corrosion requires a comprehensive visual inspection of the PCB assembly, focusing on the presence of discolouration, oxidation, or irregularities on the metal surfaces and traces.
PCBs affected by corrosion typically exhibit visible signs of surface degradation, including rust-colored deposits, greenish discoloration, or pitting on the metal components, indicating the presence of oxidized or deteriorated surfaces.
Utilizing magnification tools, such as magnifying lenses or digital microscopes, can aid in the accurate identification and assessment of corrosion-related issues during the inspection process.
Best Practices for Managing Corrosion:
To manage the risks of corrosion and preserve the integrity of PCB assemblies, implementing targeted best practices and preventive strategies is essential throughout the manufacturing and assembly processes.
Incorporating comprehensive environmental control measures, such as maintaining controlled humidity levels, implementing moisture-resistant storage solutions, and utilizing effective conformal coating materials, can aid in preventing the onset and spread of corrosion, ensuring the long-term reliability and performance of the PCB assemblies.
Conducting regular environmental monitoring and testing to assess the presence of moisture, pollutants, or reactive chemicals in the assembly environment can aid in the early detection of potential corrosion-related risks and the prompt implementation of corrective measures.
Additionally, integrating advanced protective coatings and surface finishes, such as gold plating or immersion tin coatings, can enhance the resistance of the PCB surfaces to environmental factors and reduce the susceptibility to corrosion, contributing to the production of high-quality, reliable PCB assemblies and electronic products.
Conclusion:
In conclusion, comprehensively understanding the challenges of corrosion in PCB assembly is pivotal for preserving the reliability and performance of electronic devices and systems.
By addressing the root causes, assessing the implications, and adopting best practices and preventive strategies, manufacturers and electronics enthusiasts can significantly enhance the protection and resilience of their PCB assemblies, contributing to the development of robust, high-functioning electronic applications and technologies.